![]() |
Production of construction glass at a company in Binh Duong Province. (Photo: SGGP) |
Offering discount to reduce inventory
Cement, tiles, and construction glass are three products that the Ministry of Construction listed on the red alert category because of oversupply. Up to now, the total number of cement production lines has reached 85, with a total production capacity of over 100 million tons per year, whereas domestic consumption is only 62 million tons per year.
According to the Vietnam Cement Association (VNCA), the domestic consumption market has slowed down, making the competition among domestic enterprises increasingly tense. Meanwhile, although export activities are favorable, they are unsustainable, and the efficiency reduces. For instance, in 2018, cement exports reached 31.6 million tons but only earned nearly US$1.25 billion, and the average unit price was less than $40 per ton. In 2020, cement exports hit 38 million tons, but export prices even decreased, merely at $37 per ton.
Currently, China and the Philippines are the main consumption markets of the domestic cement industry. However, it is risky when depending too much on these two markets because when they adjust their import volume, cement manufacturers will be unable to handle the situation. Not to mention that many Chinese and Thai enterprises are studying Vietnam's cement industry with the desire to contribute a certain percentage of capital to private companies to facilitate the export of cement to their countries.
The fate of the construction glass industry is also gloomy, with an excess supply of about 80 million square meters. Specifically, the production of construction glass reached about 280 million square meters last year, but the consumption of flat glass was only 200 million square meters. Currently, some glass manufacturing enterprises have had to suspend production on some lines.
Similarly, as for ceramic tiles, by the end of last year, there were 83 factories across the country, with a total capacity of about 826 million square meters per year. Nevertheless, they produced only 560 million square meters and consumed 465 million square meters. The excess of hundreds of millions of square meters has forced enterprises to find ways to sell their products, leading to cutthroat competition. The report of CMC Joint Stock Company, an enterprise specializing in producing construction materials, shows that its revenue and profit reduced by 14 percent and 26.7 percent last year, respectively, compared to 2019.
"Besides the pandemic, oversupply has caused price competition to happen fiercely. Factories have vied each other to lower prices to cut losses to reduce inventories, leading to poor business results," a representative of the Sales Department of CMC Company said.
Tightening rampant investment
The ceramic tile industry is also facing difficulties right on home ground when foreign products enter the domestic market heavily, without being strictly controlled in terms of quality and price.
According to the Vietnam Building Ceramic Association, currently, Vietnamese ceramic products exported to countries in the ASEAN must apply for a sublicense to certify the quality in each country, while it does not require certification for goods from other countries to enter the Vietnamese market.
For example, at present, China and India are the two leading ceramic tile manufacturers in the world, with the ability to supply nearly 80 percent of the world's output. Manufacturers in these two countries, especially from China, always find ways to push goods to Vietnam, even resorting to tax evasion and commercial fraud. For many years, Chinese ceramic tiles have accounted for 20-25 percent of the Vietnamese market with extremely low prices, causing domestic products to struggle.
According to the Vietnam Construction Material Development Strategy for the period of 2021-2030, with a vision to 2050, the total investment capacity of all these three products has approached the target of 2025. Amid this situation, enterprises have had to compete at all costs to sell their products, leading to low business efficiency.
Therefore, according to many experts, ministries and agencies need to consider carefully when continuing to license investment projects relating to the production of these three construction materials. For the domestic market, the investment and development of construction materials, cement, ceramic tiles, and construction glass industries must strictly comply with the investment policy following the Vietnam Construction Material Development Strategy to avoid the situation in which supply continues to far outstrip demand.
![]() |
At a recent meeting, Deputy Minister of Construction Nguyen Van Sinh said that with the current situation of the cement, ceramic tiles, and construction glass industries, localities need to consider carefully when they approve the investment policy for production projects to avoid rampant investment, leading to oversupply and waste of social resources. Especially for the cement sector, it is essential to comply with Directive No.38/CT-TTg dated September 29, 2020, by the Prime Minister, to limit the investment in the expansion and capacity increase of cement projects in large cities, densely populated areas, landscaped areas, and the natural environment that need protecting.
|
Source: SGGP
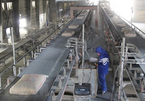
Construction materials market flourishes again
After a gloomy period due to the COVID-19 pandemic, the construction materials market in HCM City started to flourish again in the third quarter as the peak construction season began and demand from some export markets recovered.