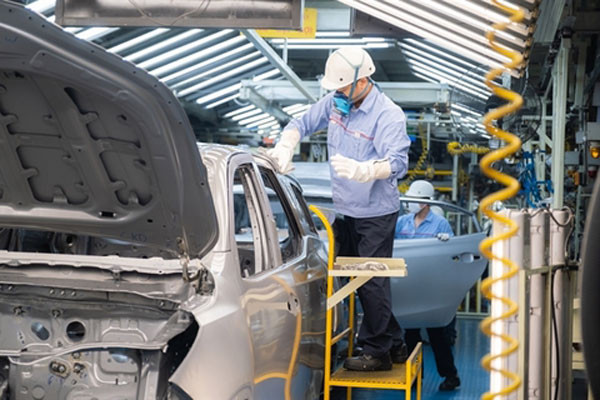
At the online trading session on supporting industry Vietnam and Japan 2022 on Tuesday, Vu Ba Phu, director of the Trade Promotion Agency from the Ministry of Industry and Trade (MoIT), said: “Over the years, supporting industry enterprises of Japan and Vietnam has been improving its production capacity and participating more and more deeply in the global production chain.”
Phu added that the number of enterprises operating in the supporting industry accounts for nearly 4.5 per cent of the total number of enterprises in the processing and manufacturing industry, creating jobs for more than 600,000 employees, accounting for 8 per cent of the total labour force in the processing industry.
He said some Vietnamese component manufacturing enterprises have quite good capabilities in such areas as manufacturing moulds of all kinds such as bicycle and motorcycle components, standard mechanical components, power cable, plastic components of technical rubber and tires.
“But the number of Vietnamese enterprises becoming suppliers of supporting industrial products for Japanese enterprises is limited,” he said
At the session, Akutsu Michio, an expert of the Japan Trade Advisors Association, said: “First, the labour productivity of local workers in Vietnam is still low.”
The expert quoted Jetro’s report, saying the labour quality rate only reached 14.4 per cent, adding: “It is a matter of concern.”
He said Vietnamese talent with high technical skills attracted by FDI enterprises went abroad to work, leading to a shortage of good human resources in the local companies.
He added that the financial capacity of Vietnamese enterprises was still weak while the assessment of capital was also tricky; as a result, enterprises found difficulty finding raw materials at competitive prices and a lack of information from foreign suppliers.
Truong Thi Chi Binh, General Secretary of the Vietnam Association of Supporting Industries (VASI), said: “Viet Nam currently has six priority industries to develop supporting industries, including electricity, electronics and mechanical engineering.”
Binh said among the mechanical engineering industry, the motorcycle manufacturing industry, whose output has decreased in the past year to 2.5 million vehicles per year, still has the best production and localisation rate as well as the participation of Vietnamese enterprises in all supply layers, product classes such as electricity, electronics, rubber and plastic.
Next was the automotive industry which stood out with the Toyota brand. The output of the industry was much lower than that of the motorcycle industry, said Binh, adding it was the reason why the auto industry had a low domestic rate and rarely had the participation of Vietnamese enterprises.
According to Toyota, last year, its sale reached 96,000 vehicles in Vietnam, of which 44 per cent were assembled domestically with different models.
Binh from VASI considered Vietnamese enterprises could only supply plastic components to car companies because these are bulky components and have large logistics costs, so they were forced to be localised.
At the session, experts said though the mobile phones industry accounts for nearly 20 per cent of the export share of industries, the contribution in mobile phone components of Vietnamese enterprises were still plastic and rubber as electronic components were supplied mainly by FDI enterprises, said the VASI leader.
Binh said: “Vietnamese enterprises are currently only able to produce single components, but have not yet been able to produce components apart from some machinery in the construction industry.”
“In the last 5 years, the movement of factories producing supporting industrial products to Vietnam has been clear. To support businesses, the association has focused on finding solutions to move forward in the supply chain by forming business groups and sector groups to focus on increasing the quantity and quality of production.”
She added that the supply chain shift from China would bring more orders, which could be larger than the number of products domestic enterprises were producing in Vietnam.
Binh said VASI started forming a business group to produce components, hoping to create the first example and participate more deeply in the supply chain of public products.
Mentioning solutions to overcome the weaknesses of Vietnamese suppliers, Akutsu Michio said: “Vietnam can take advantage of the commercial companies, which can supply raw materials at competitive prices, assist in customs clearance, propose new production methods, mechanise and automate for manufacturing and assembly enterprises.”
“If something goes wrong, they coordinate with the supplier and the assembly plant to propose a solution. Moreover, they can provide information that is not publicly available on the Internet such as on capital investment, and new product development programmes.”
Source: Vietnam News