![]() |
Since COVID-19 broke out, many firms have shifted to manufacturing medical face masks
|
Since the virus outbreak, masks have become the most sought-after protective gear, in addition to disinfectants and protective overalls. The pandemic drew about 3,000 more enterprises on board to produce masks, many of which have been operating outside the textile and garment sector. Chinese electric car maker BYD Co., backed by Warren Buffett, said it became the world’s largest face mask maker after starting production less than a month ago.
According to Xinhua, BYD repurposed its 1,500-square-metre electronic production factory in the Baolong Industrial Garden in the southern metropolis of Shenzhen, Guangdong province for packaging and examining masks with more than 600 workers and 100 production lines.
Li Wei, BYD president, said the corporation decided to produce masks by itself as it was under pressure to resume work and the demand for masks has been soaring. The company has 250,000 employees, and if it prepares two masks for each, they would need 500,000 masks a day. Also, Shenzhen has more than 20 million people, who would need more than 40 million masks.
With the new production lines, BYD can make five million masks and 300,000 bottles of disinfectant a day, making the company become the biggest mask manufacturers in the world.
SAIC-GM-Wuling, General Motors’ light-vehicle joint venture with SAIC, has also been quick to jump on the bandwagon. It is the first auto manufacturer to build machines to produce face masks, helping China to combat the deadly coronavirus outbreak. Along with face masks, it manufactures additional machines to ramp up its output of other protective gear, the representative of the company said on social media.
Some companies in Hong Kong (China) such as New World Development Co., Ltd. and the owner of Hong Kong Television Network Mall have also stepped into the game, frustrated by the breakdown in the supply chain in China after various lockdown measures crippled the logistics sector.
According to Yahoo! Finance, Honeywell International Inc.has been taking pro-active steps to expand manufacturing of N95 face masks at its Smithfield, Rhode Island facility and will deliver masks to the US Department of Health and Human Services to boost the US stockpile. This move will support the US government’s efforts to protect people with the use of personal protective equipment.
Quality concerns
Despite being introduced as anti-virus protective gear, many of the major products in the market do not meet the medical face mask standards published by the Vietnamese Ministry of Health. Specifically, each medical face mask has to contain a bacterial filtration layer that is not manufactured in Vietnam.
According to Nguyen Huu Phuc, general director of a local face mask manufacturer Como Ltd., truly medical face masks are scarce in Vietnam as there is no local capability to produce these layers. However, the items consisting of two simple layers of cotton that are in abundance in the market cannot prevent virus infection as advertised.
Indeed, face mask production lines in China are also struggling with the same quality problem. With the great leap in demand for the products due to the COVID-19, since February, the country has been producing 200 million products a day. However, not even this capacity can meet local demand and global orders.
Factories that once made shoes, iPhones, and cars have shifted to making face masks. Machines that once churned out fabric materials are now producing materials for masks. Currently, of the hundreds of millions of masks the country makes a day, only 600,000 are N95 standard, according to the National Development and Reform Commission of China. The nation’s authorities have been constantly licensing dozens of factories to accelerate production.
However, the efforts of the Chinese government seem to be hopeless as the supply of bacterial filtration layers or melt-blown fabric is falling short, just like in Vietnam. The machine that creates this fabric melts down plastic material and blows it out in strands, like cotton candy, into flat sheets of melt-blown fabric for face masks and other filtration products. A similar line of machines can create a related kind of fabric, called spun-bond fabric, also used in face masks and medical protection suits worn by healthcare workers, according to newswire NPR.
Chinese companies produce nearly three million tonnes of non-woven fabric a year, according to the China Nonwovens and Industrial Textiles Association. Less than a single per cent of that is melt-blown fabric.
Far from sustainable investment
From previous outbreaks like SARS in 2002, H1N1 in 2009, and Ebola in 2014, it can be seen that the average timeline for an epidemic to blow over is one or two years. The COVID-19 outbreak may have a similar duration. Thus, such great investments in face mask manufacturing lines may not be wise for investors.
There are also concerns about a possible oversupply situation. The Ministry of Industry and Trade stated that local textile companies will offer about 30 million face masks to the market in the middle of April. China also makes about 200 million items a day, according to NPR.
Along with textile and garment firms, electronic giants like Japan-based Sharp and China-based Foxconn are also pursuing plans to develop large-scale production lines for medical face masks. Sharp will refurbish one of its television factories to manufacture 500,000 items a day, while Foxconn has committed to producing 2 million face masks every day.
Consequently, as major companies shift their business and the epidemic may only last for one or two years, the question to answer is how the world will deal with the tremendous surplus of face masks after the crisis.
More seriously, most products in the market are single-use and made from polypropylene – and each mask is wrapped in plastic. This also poses significant environmental issues.
According to Austria-based textile company Leizing Group, global garment output in 2015 reached 95.6 million tonnes of goods that cost about 2 trillion gallons of water and 145 million tonnes of coal.
The textile and garments industry is supposedly one of the most polluting industries as it demands copious amounts of water, energy, and chemicals to produce fabrics. Moreover, manufacturing activities also release wastewater, gaseous waste, and solid waste.
As the epidemic keeps spreading and major antiviral face masks have yet to qualified the standard, pouring capital into manufacturing masks could do more harm than good. Hence, investment in face mask production is far from sustainable. VIR
Van Anh
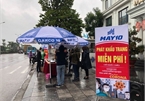
Garment 10 to produce medical face masks, first export order worth US$52m
Garment 10 Company was investing in producing medical face masks as well as cloth masks with ten production lines being installed, the company’s director Than Duc Viet said
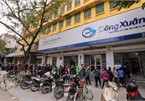
Garment firms shift to produce antibacterial masks to meet demand
Amid the coronavirus epidemic, many textile businesses in Vietnam have shifted to producing antibacterial masks to serve market demand.