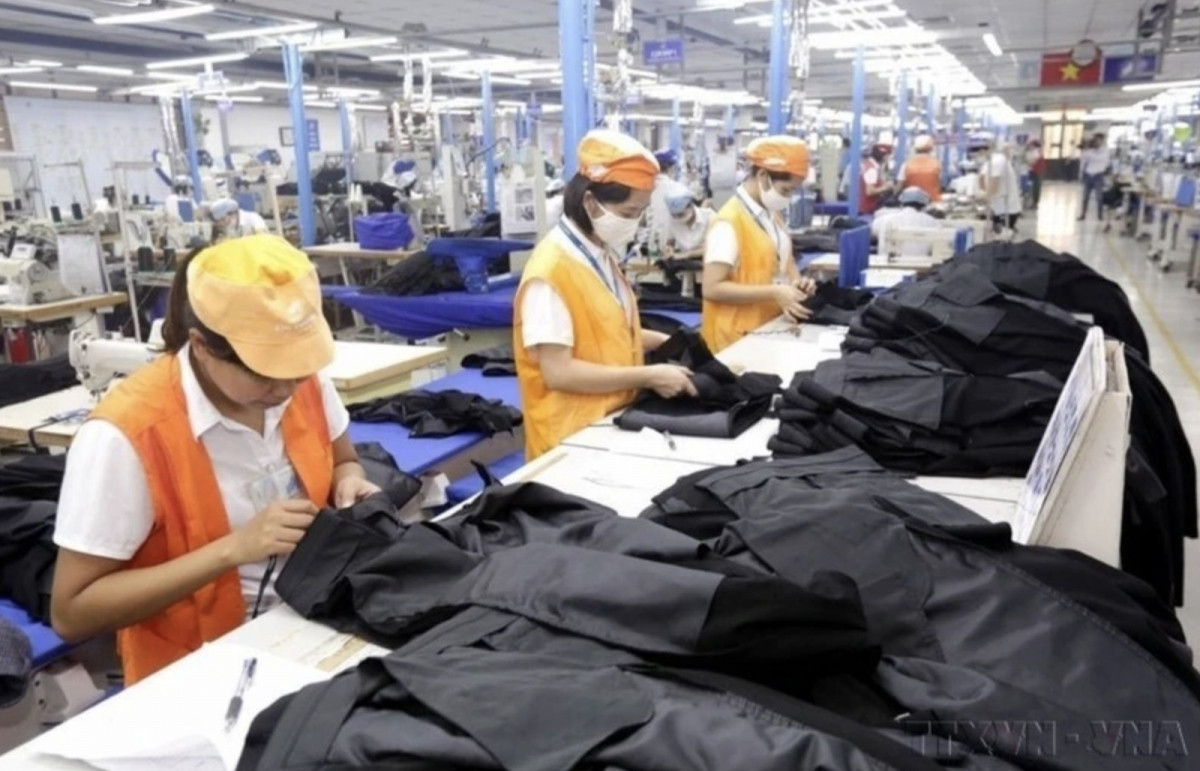
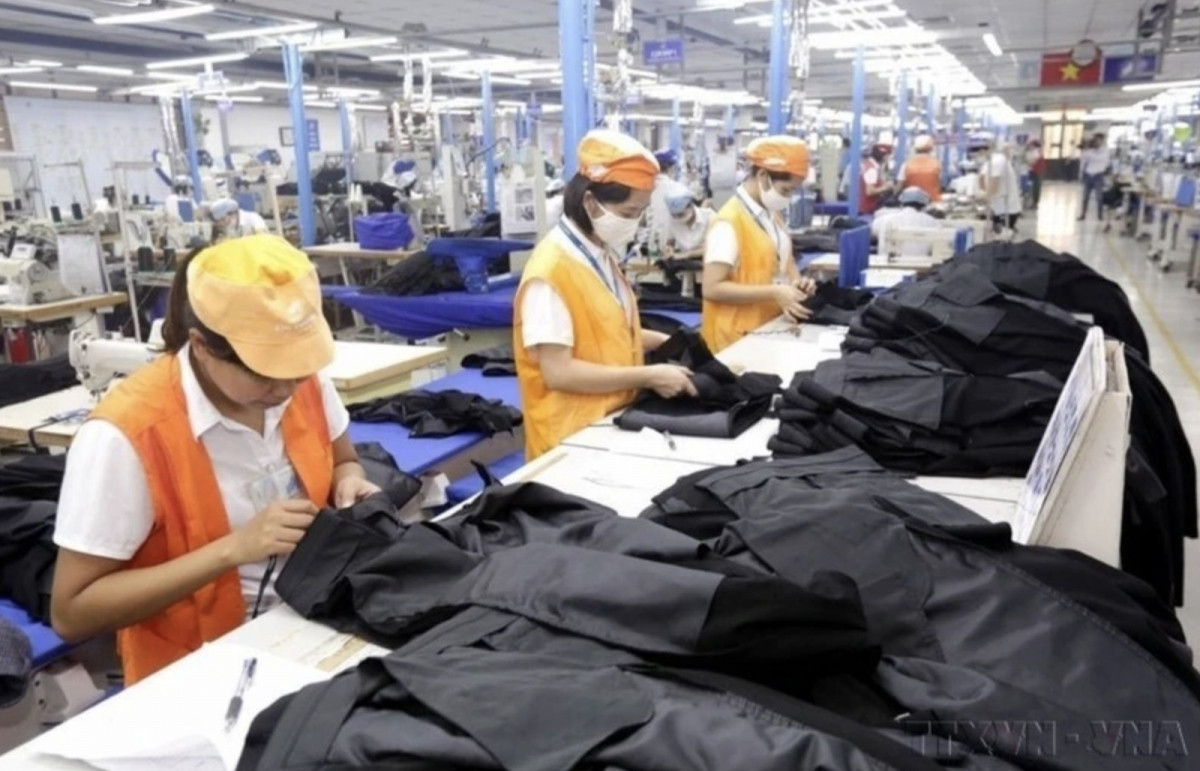
Qualitative demands for greener practices are increasingly being quantified through policies targeting manufacturers and consumers, particularly regarding taxes as well as waste and emission management.
The European Union (EU), one of the main export markets for Vietnam's textile-garment industry, is vigorously pursuing the European Green Deal, aiming to reduce net emissions by 55% by 2030 compared to the 1990 level and achieve carbon neutrality by 2050.
According to the Ministry of Industry and Trade, the strategy serves as a pillar within the industry, guiding the EU in revising new regulations in various sectors. For the textile and garment industry, key regulations include the ecodesign requirements for sustainable products, waste directives, and extended producer responsibility programmes.
Facing these new demands and challenges, May 10 Corporation has been greening its production processes for about three years by investing in modern machinery and equipment that consume less electricity. While making significant expenditure on solar energy systems and rooftop power, the company has integrated supply chains within Vietnam and abroad to maximise the use of recycled and natural materials and ensure that the fibre content in their products meets customers' requirements for origin.
General Director of May 10 Than Duc Viet underscored that greener production is no longer a choice but a mandatory requirement. The gradual adaptation of Vietnamese enterprises will facilitate sustainable export practices.
The garment company is also transitioning from coal-based fuels to biomass electricity to minimise carbon emissions. By 2024, if all of its projects become operational, May 10 expects to reduce the emissions by more than 20,000 tonnes annually.
Currently, the Vietnam National Textile and Garment Group (Vinatex) is implementing carbon reduction solutions by measuring the carbon footprint across product life cycles and developing a green, circular production strategy. So far, the group's members have reduced electricity consumption per product unit by 2% compared to 2022.
However, according to the Vietnam Textile and Apparel Association (VITAS), domestic legal frameworks remain limited, with no specific policies or regulations for the sector regarding the circular economy. Regulations on greenhouse gas inventory and carbon taxes are lagging behind international timelines.
VITAS Deputy Secretary General Nguyen Thi Tuyet Mai noted that major global fashion brands have been increasingly prioritising green enterprises or requiring suppliers to adopt green practices. This approach not only protects their reputation and business philosophy but also complies with increasingly stringent regulations.
However, the reality is that meeting green standards in the textile industry requires substantial conversion costs and long transition periods. Most Vietnamese textile exporters are small- and medium-sized enterprises, therefore their switching of internal control systems and conduction of greenhouse gas inventories need to be faster and more cost-effective.
"Green transition is an inevitable path – a game we have no choice but to play," Mai said. Yet, more than 80% of small and medium enterprises in the sector currently lack the capital needed for green production transition.
To cope with these challenges, in the short term, enterprises are advised to continue to operate flexibly, seizing market opportunities and focusing on technically demanding, small-batch, high-value-added products rather than low-cost, popular items that are difficult to compete with.
VOV