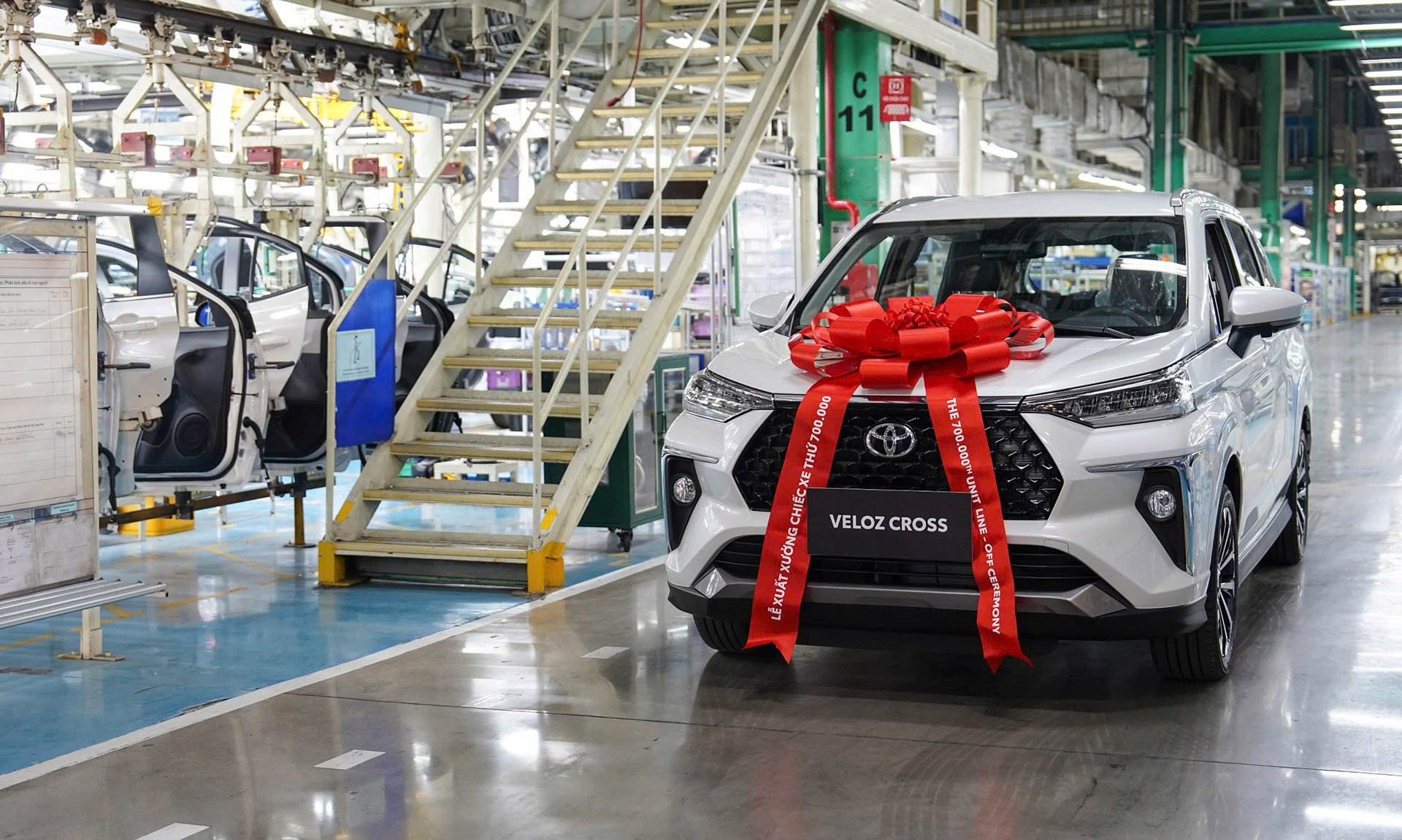
Toyota Vietnam has recently celebrated the production of its 700,000th car, making it the largest automobile manufacturer in the country since obtaining its investment license in 1995. The 700,000th car, a Toyota Veloz Cross, achieved a localization rate of approximately 38%.
Since its establishment, Toyota's production capacity at the Vinh Phuc plant has grown significantly, from an initial average of 2 cars per day (212 cars per year) to more than 108 cars per day, equivalent to around 27,000 cars annually.
A leader in production but still short on localization
Toyota Vietnam currently offers around 15 car models in the domestic market, with 10 of them being imported from Indonesia, Thailand, and Japan. Only 5 models are produced and assembled locally.
Among them, the Toyota Vios has the highest localization rate at 43%, making it the company’s best-selling model.
The Innova and Veloz Cross models follow with localization rates of 37-38%. In contrast, the Fortuner and Avanza Premio models have significantly lower localization rates.
According to the Ministry of Industry and Trade’s Department of Industry, the average localization rate for passenger cars under nine seats with internal combustion engines in Vietnam ranges from 7-15%.
Ford achieves about 10%, while some models by Thaco reach 15-18%.
Although Hyundai aimed for a 45% localization rate by 2021, no recent data has been disclosed. On the electric vehicle front, VinFast reported a localization rate of around 60% as of 2024.
Despite Toyota's relatively high localization rate compared to other manufacturers, it remains significantly lower than the targets set out in Vietnam’s Automotive Industry Development Strategy by 2025, with a vision to 2035.
The strategy, outlined in Decision No. 1168/QĐ-TTg (July 16, 2014), aimed for a localization rate of 30-40% by 2020 and 40-45% by 2025.
Localization barriers and industry challenges
Toyota’s initial commitment in 1995 was to achieve a localization rate of 30-40% within 10 years. However, by 2015, only the Innova model had reached 37%, while other models fell far behind with an average rate of just 2.7%.
The primary obstacles to meeting localization goals include the limited market size and the underdeveloped domestic automotive supporting industry.
To address this, Toyota has partnered with the Department of Industry under the Ministry of Industry and Trade to support local manufacturers in improving production processes and integrating into the global supply chain.
Currently, Toyota Vietnam collaborates with 60 suppliers, 13 of which are Vietnamese-owned while the rest are foreign-invested enterprises (FDI).
The company sources approximately 1,000 different types of components from these suppliers, mainly including plastic and rubber parts, as well as molds for manufacturing components like bumpers and seats.
During the ceremony to mark the production of the 700,000th car, Tran Duy Dong, Chairman of Vinh Phuc Provincial People’s Committee, called on Toyota Vietnam to increase collaboration with local suppliers in the automotive supporting industry.
He also urged the company to develop a transition strategy toward hybrid and electric vehicles, aiming for the production of intelligent, eco-friendly transportation solutions.
As Toyota Vietnam moves forward, strengthening its localization efforts remains crucial to maintaining competitiveness and meeting national strategic goals in the rapidly evolving automotive landscape.
Pham Huyen