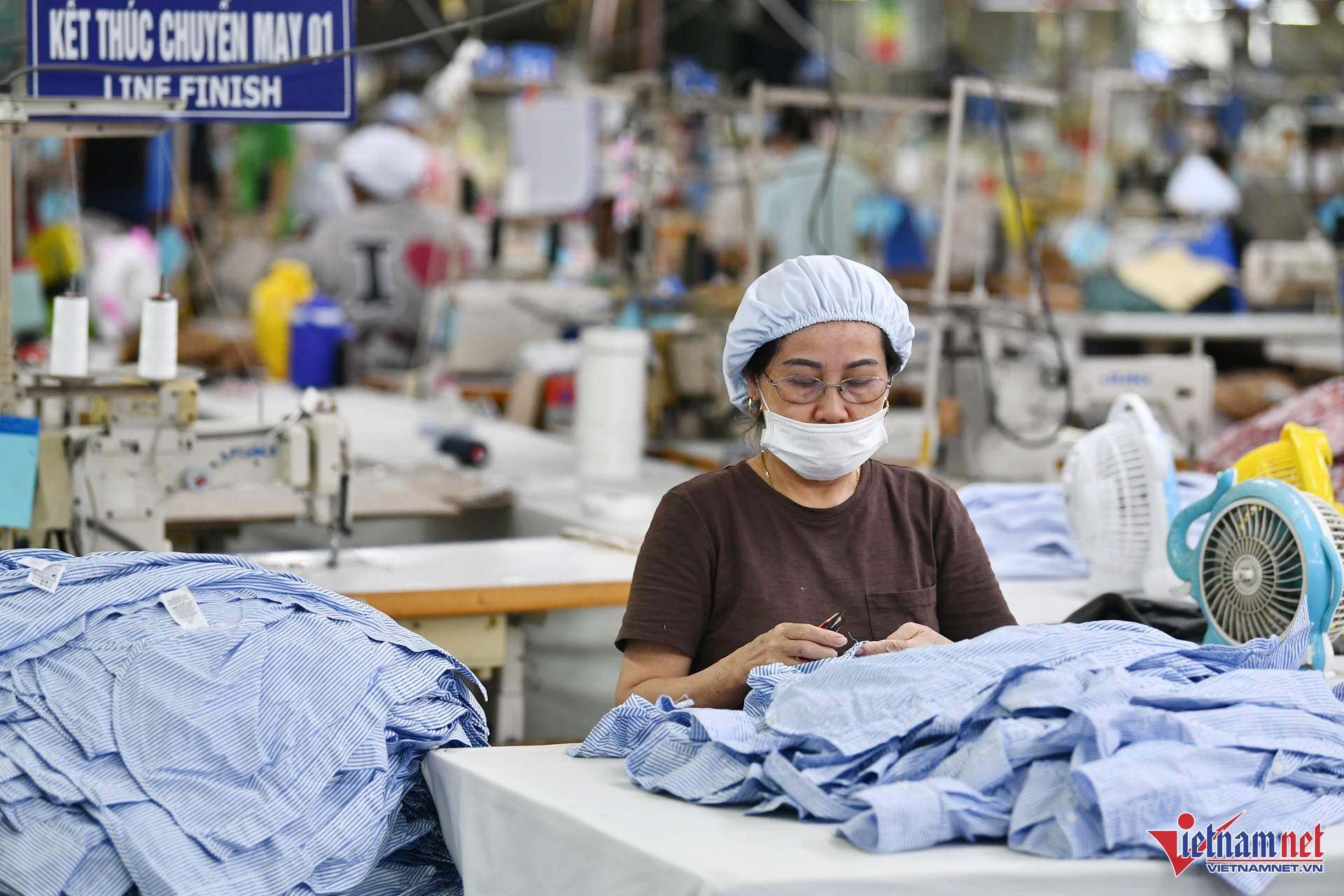
In the last three years, the world’s textile and garment market witnessed a sharp fall in total demand because of recessions and epidemics.
In 2023, the total demand for textiles and garments decreased by 5 percent because of geopolitical conflicts and consumer decline due to high inflation and interest rates.
In such conditions, the world’s top garment exporters such as China, Vietnam and India saw export turnover decline sharply.
Surprisingly, Bangladeshi textile and garment exports still grew well and even made a record in textile and garment exports with turnover of $4.6 billion a month (November-December 2022).
In 2020, Bangladesh was in the third position in the world in terms of textile and garment exports, after Vietnam and China, with export turnover of $29.8 billion. And just two years later, it jumped to second position with $49 billion, a sharp growth rate of 64 percent.
Explaining the ‘Bangladesh phenomenon’, Le Tien Truong, chair of Vinatex, the largest textile and garment producer in Vietnam, said since 2018, the country has spent big money to organize production under the best, most modern conditions to satisfy the highest requirements and standards.
As of August 2024, there were 230 factories with LEED (Leadership in Energy and Environmental Design) certificates, and 40 percent of the factories had LEED Platinum, the highest standard for green production set by USGBC (US Green Building Council). Meanwhile, another 500 garment factories were awaiting assessment and certification for meeting LEED.
The green production, implemented with labor stabilization and quality and productivity improvement, plus the advantage in cheap labor force, all helped Bangladesh maintain its growth.
Truong believes this is a big lesson for Vietnam.
In Vietnam, the factories meeting Green Platinum standards are mostly foreign invested (FIEs), and Vietnamese large companies such as Viet Tien. To date, 619 works in Vietnam have LEED certificates, but only 10 percent of them are textile and garment works, while there are 13,000 textile and garment companies with over 50,000 factories nationwide.
Truong noted that the figures are modest compared with the scale and the requirement set for the industry.
Building and renovating factories to obtain green and sustainable certification remains a big challenge for businesses because of financial investment requirements (factory area, auxiliary areas, roof area using solar power, fresh air volume, greenery ratio within factories’ campuses, and paint colors which help workers not to feel psychological pressure after 8-9 hours of work.
Green production
As one of the industries which produce big volume of waste with over 100 billion products each year, the solid waste volume from textiles and garments is over 90 million tons, while the figure is expected to increase to 150 million tons by 2030. Of this, only 20 percent is recyclable.
Therefore, large fashion companies around the world have been responding to the emission reduction programs, with the net-zero goal by 2050.
H&M, Levis, Uniqlo and Zara all have set goals. H&M, for example, wants to have 30 percent of materials to be from recycled sources by 2025. The figure would be 50 percent by 2030.
As for Adidas, the manufacturer is determined to have half of its products made from recycled materials.
To date, there has been no regulation about the mandatory ratios of recycled materials in textile and garment products. However, green production is a must. The regulations to legalize the green production strategy will come out, sooner or later, especially in developed countries.
Therefore, both buyers and manufacturers are preparing for green production, so that when green standards are legalized, their supply chains will not be interrupted and disrupted.
In Vietnam, the process is predicted to last 5-10 years. Truong stressed that if Vietnam doesn’t enter the transformation process immediately, Vietnam’s products won’t be able to exist in the market, once the green criteria and standards are legalized.
To maintain sustainable development in the next decades, textile and garment companies have no other choice than making big investments to develop green and sustainable production now.
In 2021-2024 Vinatex focused on renovating yarn manufacturing technology and energy for production. This has helped reduce 20 percent of electricity volume consumed per kilogram of yarn, from 3.4 to 2.8 kwh per kilogram. Meanwhile, in the dying industry, the volume of water used for one square meter has decreased by 15 percent.
Ngoc Ha