At the Vietnam Business Forum (VBF) which took place in late 2019, the working group about automobiles and motorbikes pointed out that Vietnam’s automobile industry is slowly developing because of low output, weak high-quality material industry and limited management capability.
According to the working group, Vietnam’s car parts are three times more expensive than Thailand’s. Domestic manufacturers, for example, quote a price of nearly $4 for each product. The 200-300 percent price gap is also seen for plastic components, which is even higher than high-quality components.
The mass car imports have caused difficulties for domestic production. Automobile joint ventures have ceased assembling many models in Vietnam and import products instead. This is one of the reasons behind the weak supporting industries.
![]() |
The mass car imports have caused difficulties for domestic production. Automobile joint ventures have ceased assembling many models in Vietnam and import products instead. This is one of the reasons behind the weak supporting industries. |
Meanwhile, experts pointed out that if supporting industries cannot develop, Vietnam’s automobile industry will just do simple assembling forever.
According to Toyota Vietnam’s general director Toru Kinoshita, the high output and large market are the most important factor to persuade automobile manufacturers and suppliers to increase the localization ratios.
Japanese Enkei came to Vietnam in 2007 and became the car part supplier of Toyota, Truong Hai, Honda, Nissan and Mitsubishi. Its major product is casting rim and it only makes 24,000 products a month.
Meanwhile, the company needs to have orders for 100,000 products a month to optimize production. With current small orders, each product has a production cost 5-10 percent higher than other regional countries.
In its report about the implementation of the plan to develop the automobile industry released in 2019, the Ministry of Industry and Trade (MOIT) admitted that Vietnam failed to meet the goals set for the automobile industry.
Vietnam wanted to have the localization ratio of 60 percent of cars with nine seats or less, while the real ratio is 7-10 percent only.
Vietnamese enterprises can only make very simple car parts, such as tyre, glass, battery and plastic products. At least 80-90 percent of major materials for making components, such as alloy steel, aluminum alloy, plastic particles and technical rubber, must be imported.
Tran Huu Nhan from the HCM City University of Science andTechnology, commented that Vietnam is still doing the welding, painting, assembling and testing, i.e. the world’s technologies of 1940s, 1950s. The biggest problem for Vietnam’s automobile is the limited demand.
Meanwhile, Nguyen Khac Trai, former lecturer of the Hanoi University of Science and Technology, said in the current conditions of Vietnam, it will not have an automobile industry of its own.
“I think Vietnam needs 20 more years,” he said.
Tran Thuy
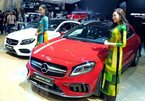
Govt’s new decree removes barriers to automobile imports
Automobile importers in Vietnam will no longer have to obtain a Vehicle Type Approval (VTA) certificate from authorities in exporting countries, making it easier for them to import cars into the country.
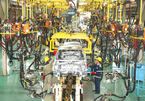
Vietnamese automobile makers ask for more support
Among the incentives, the government is urged to lower the special consumption tax for locally made parts to help them reduce prices to compete with foreign manufacturers.