![]() |
Businesses are being forced to think outside the box in establishing new links in global value chains
|
Closed-off ports and border gates, and delayed shipments from China are not only affecting Chinese companies but also global groups that depend on supplies to keep business running, including operating enterprises in Vietnam. Businesses large and small are struggling to circumvent the epidemic so as to ensure production materials in the next few weeks.
A representative of Intel Group’s $1 billion chip plant in Ho Chi Minh City admitted the company had a plan to proactively respond to such situations, so the group has not yet been affected by the outbreak in terms of raw material supply disruption. However, it admitted their production lines could face not running a full operation if the situation does not improve in quick fashion.
Intel is not the only one facing a hard time. A range of foreign-invested enterprises have raised their voices regarding the same issue, including LG, Samsung, Formosa, and Foxconn, explaining that they may cut some production lines in the meantime.
US tech giant Apple was expected to increase exports in Vietnam by 30 per cent this year, but its output depends on outsourcing companies such as Samsung, Foxconn, and LG, so the lessened output of these groups will affect Apple’s export volume in Vietnam.
The aforementioned businesses contribute much to Vietnam’s total export growth. According to the General Statistics Office, the country’s total export-import value with China accounted for a very large ratio of total exports in 2019, of which exports to China accounted for 15.75 per cent while imports were 29.7 per cent. On that basis, the COVID-19 outbreak could affect the production of key export products that heavily depend on imported materials such as cellphones and their electronic components, computers, textiles, and footwear.
Preparing for disruption
For a short-term plan to ensure exports in time, enterprises must find a replacement market for raw materials such as from South Korea, Thailand, or India although it is certainly not an easy task, adding cost and time.
Nguyen Chi Trung, chairman of leading leather firm Gia Dinh Group JSC, said that to respond to the worst case scenario, his company is considering importing raw materials from other countries such as South Korea, Japan, and Bangladesh to compensate for the shortage for production.
Elsewhere, Nguyen Quoc Anh, chairman of the Rubber Plastic Manufacturers Association, said that enterprises that produce rubber and plastic components, as well as parts for foreign auto assembly lines and machinery production lines, were facing difficulties due to delayed shipments from China.
“If the situation does not improve by the end of February, our members may have to import raw materials from South Korea or Europe. That will bite into the profits of our enterprises,” said Anh.
Responding to the effects and solutions that enterprises are preparing, a representative of Canon said, “This might also affect our plans to launch new products in the market in 2020. As an immediate solution, we can only increase the volume of goods from secondary suppliers for production.”
In addition to this, the representative added, as goods transported by shipping are delayed, Canon will use planes instead, so that products can flow more easily. “However, these are only temporary measures, and we still have yet to find any long-term solutions since the epidemic situation remains complicated and unpredictable,” he said.
The Ministry of Industry and Trade suggested that companies should use the crisis to seek new markets and suppliers to manage future risks if the virus situation cannot be solved within a month. Business leaders could also conduct a scenario-planning exercise and develop action plans, making now the time to discover or develop alternative sources and diversify value chains.
Developing local supporting industries
The supporting industry plays a role as an essential foundation to improve competitiveness of industrial products.
According to Reed Tradex, the largest organiser for supporting industry exhibitions in the ASEAN region, apart from challenges caused by world economic instability such as flexible exchange rate policies and strict regulation and monitoring in financial systems, the trend of production relocation from China to Vietnam is also bringing a host of opportunities to businesses that keep informed with the latest developments. However, one of the most important things is that Vietnam needs to quicken its construction of supporting industries.
Do Thi Thuy Huong from the Vietnam Electronic Industries Association said that to join the global value chain, businesses should be interested in establishing links, and connecting with domestic enterprises as well as global enterprises.
“If Vietnam’s electronics industry and supporting industries can build a supply network and create products that meet international standards, it will sharply improve competitiveness and the ability to join in with the entire supply chain,” Huong said.
For instance, to reap the benefits posed by the free trade agreements, the leather and footwear sector needs to develop a supporting industry to reduce reliance on the import of raw materials, enhance competitiveness, and boost high-value exports.
This is because new-generation agreements set strict requirements on product origin, a big challenge for Vietnamese enterprises in textiles, garments, and footwear as they are heavily dependent on material sources imported from China.
Vietnamese exporters have been advised to continue promoting the supporting industry, and ensure the origin of raw materials for production.
Sami Kteily - Executive chairman PEB Steel
China’s economy today is more vulnerable than it was during the SARS outbreak in 2003 and this comes hot on the heels of the devastating US-China trade dispute. Travel bans, heightened public health measures, and the current extension of the Lunar New Year holidays has undoubtedly affected production levels and will affect economic growth in the year to come. We are concerned that if GDP growth falls below 5.5 per cent in 2020, this will have an economic ripple effect throughout Southeast Asia. When it comes to our pre-engineered steel buildings industry, adequate inventory levels play a significant role in delivering goods quickly to customers in the construction market. It is normal for companies of our size to keep a large inventory of raw materials. At PEB Steel, we always keep a minimum of three months’ stock, especially for items imported from overseas which represent around 50 per cent of our total purchases. Thanks to our 25 years’ experience in Vietnam, we tend to keep more stock than usual over the Lunar New Year holidays as we expect a drop in shipments from China during the this period. This coronavirus outbreak happened to come just after the holidays when our inventory levels are high, so we have a deep reserve of raw materials that will keep us going for several months. February shipments from China have been delayed but we will not find this crippling in the short term thanks to the high reserves that we have. In order to address similar matters in the long term, we are going to work with local suppliers to develop new supply chains or replace materials to cover the shortage. It is hard to offer an accurate prediction of the future, as the coronavirus is spreading at a rate six times faster than SARS and will likely cause numerous challenges for us and our customers. This includes global firms who rely on suppliers based in China and invest in industrial sectors, which is the most important segment of our business. Joseph Perucca - General director GIVI Vietnam
In addition to the already sad human loss, the coronavirus will have extreme repercussions in many Southeast Asian economies. A large proportion of components and materials come from China and over the next six or eight months, there could be problems in maintaining production. The current state of affairs, in conjunction with the Lunar New Year festivities in both Vietnam and China, has accelerated the inevitable problem of sustaining a large part of the economy given the absence of production of raw materials within the country. This situation will result in a long journey, since when China recovers, it is understandable that the priority will surely be to supply internal factories in order to mitigate the extreme financial loss that China is suffering due to this epidemic. VIR |
Phuong Thu
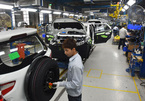
Business production hit because of lack of materials from China
Vietnam's reliance on Chinese materials has been clearly exposed during the Covid-2019 crisis, as imports from China have declined.

Material autonomy key for Vietnam to fully exploiting EVFTA
Textile stocks have been on an temporary upswing thanks to the recent ratification of the EVFTA but textile enterprises still face difficulties due to heavy dependence on imported raw materials and reduced demand worldwide.