Công ty CP Tập đoàn Kỹ Thuật và Công Nghiệp Việt Nam (Intech) có trụ sở tại KCN Lai Xá, xã Kim Chung, huyện Hoài Đức, Hà Nội. Được thành lập từ năm 2011, đến nay, Intech đã trở thành doanh nghiệp công nghiệp hỗ trợ tiêu biểu với dải sản phẩm thuộc lĩnh vực cơ khí tự động hóa, công nghệ.
Hiện công ty cung cấp các Jig, Tool, chi tiết máy trong lĩnh vực gia công chính xác; con lăn trong hệ thống dây chuyền sản xuất, hệ thống robot tự hành, bốc xếp hàng hóa trong nhà máy; cung cấp băng tải con lăn, băng tải belt … Công ty hiện có hơn 250 nhân sự với 2 cơ sở nhà máy tại Hà Nội và TP.HCM.
Năm 2024, Intech là 1 trong 5 doanh nghiệp được lựa chọn tham gia Chương trình hỗ trợ cải tiến sản xuất do Cục Công nghiệp, Bộ Công Thương hợp tác cùng Toyota Việt Nam triển khai. Thời gian thực hiện trong 6 tháng, kể từ tháng 7-12/2024. Theo đó, kết quả đạt được tại Intech rất tích cực.
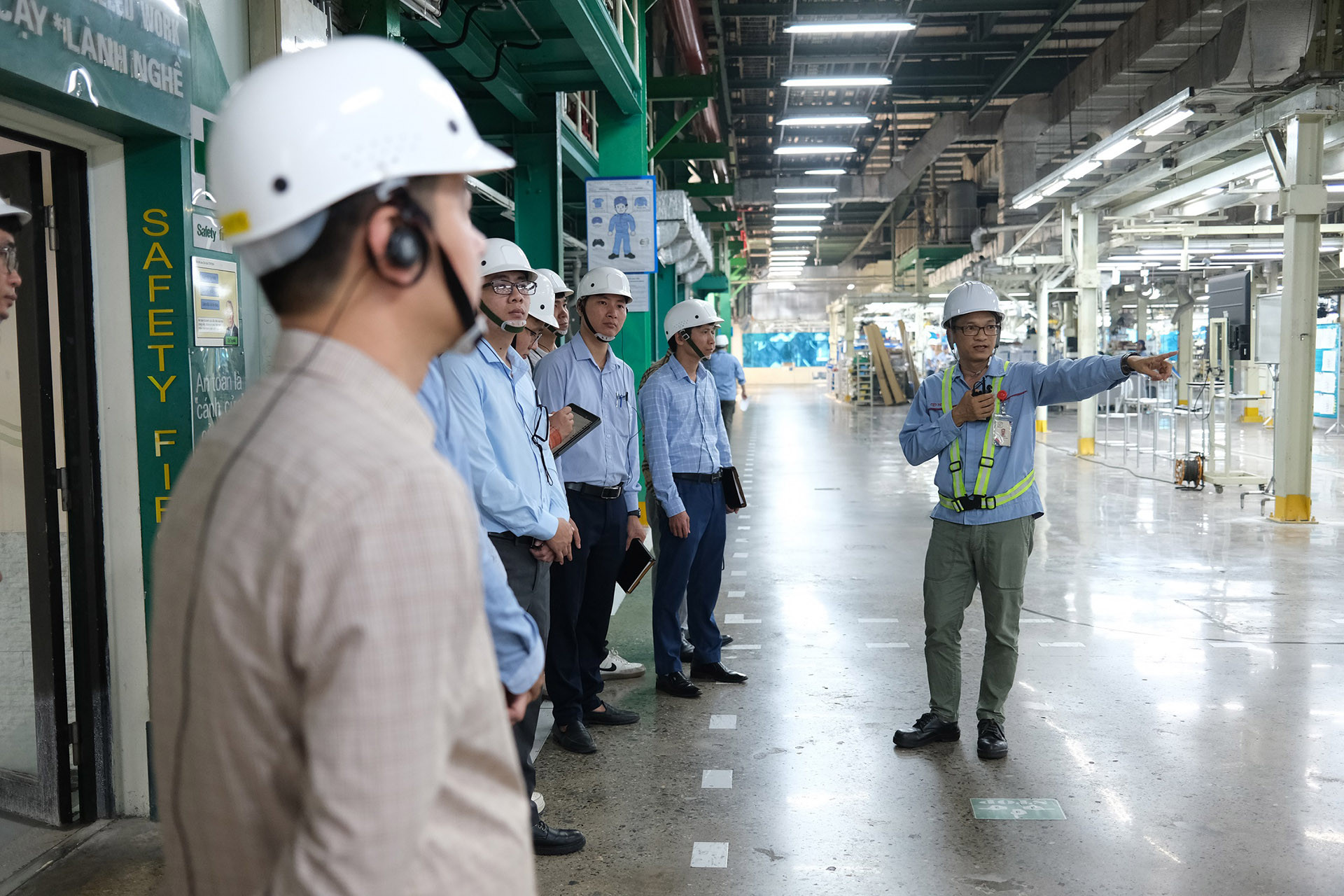
Trước khi cải tiến sản xuất, trình độ kiến thức và sự hiểu biết của đội ngũ nhân sự gần như là số 0 về vấn đề 5S (phương pháp sản xuất tinh gọn giúp cải thiện hiệu quả tại nơi làm việc và loại bỏ lãng phí), Karakuri Kaizen (một khái niệm xuất phát từ Nhật Bản, đề cập đến việc sử dụng các giải pháp đơn giản, không dùng năng lượng điện, để tự động hóa các quy trình công nghiệp)…
Việc sắp sếp nhân sự của công ty còn chưa tốt, mỗi người một máy, chưa có tiêu chuẩn cho công việc, lỗi phát sinh nhiều do yếu tố con người dẫn đến năng suất thấp. Thao tác làm việc của nhân sự cũng bất cập như thao tác nặng, công nhân phải giữ tay lâu, khó nhìn, di chuyển xa. Đặc biệt, khâu quản lý tồn kho hàng hóa khá kém, vật tư để lộn xộn, không gắn tem mác nên công nhân khó nhận diện. Hàng thừa bị tồn đọng nhiều, không được tận dụng hiệu quả. Dòng chảy sản xuất không tối ưu, đi vòng, lặp lại nhiều và các công đoạn không liên thông với nhau.
Sau khi tham gia vào chương trình tư vấn cải tiến của Toyota Việt Nam, kết quả đạt được tại Intech rất tích cực.
Ban Dự án 5S của công ty được lập ra, đã nêu ra 10 nhóm nội dung phải làm với 178 vấn đề cần cải tiến 5S. Sau 6 tháng, công ty đã hoàn thành 141 vấn đề cả tiến 5S. Công ty cũng hoàn thành 23/27 hoạt động cải tiến hiệu suất. Số nhân sự đã được sắp xếp lại, giảm đi 8 người và mục tiêu quý I/2025, công ty sẽ giảm đi 10 người. Diện tích nhà xưởng tiết kiệm 136m2.
Ước tính, giá trị tiết kiệm tại công ty Intech lên tới 916 triệu đồng/năm.
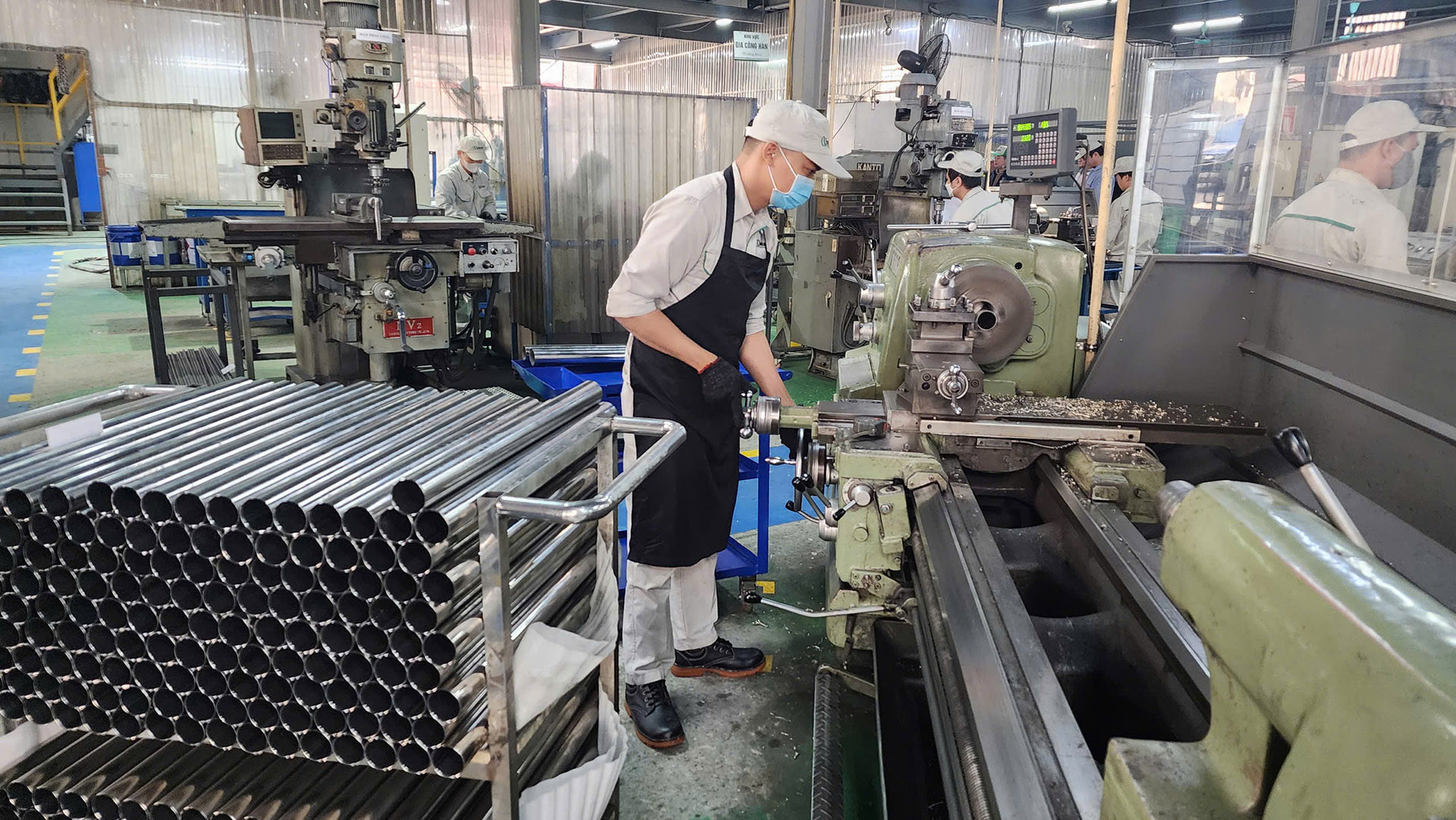
Đi vào kết quả cụ thể, Intech cho hay, trong hoạt động cải tiến Kaizen, có nhiều vấn đề đã được thay đổi so với trước. Ví dụ, công ty sắp xếp, phân loại khu vực làm việc và lối đi trong xưởng. Trước đây, đường đi trong nhà máy thường bị các xe đẩy chiếm đường đi, công nhân dễ bị gặp tai nạn nếu vấp phải chướng ngại vật. Theo tư vấn của các chuyên gia từ Toyota Việt Nam, công ty đã sơn lại đường đi bằng màu xanh lam cho nổi bật đường đi, dễ phát hiện khi có vật cản đường. Nhờ đó, công nhân viên khi di chuyển trong nhà máy dễ nhìn, dễ phát hiện khi có vật cản nhô ra đường đi, giảm nguy cơ mất an toàn khi đi trên đường bị va vào vật cản. Ý thức nhân viên được nâng cao
Ví dụ thứ hai là công ty thực hiện 5S tại khu vực giá để nguyên vật liệu và giá để linh kiện. Trước đây, khu vực này để nguyên vật liệu lộn xộn, không sàng lọc. Diện tích kho nguyên vật liệu chiếm 120m2, không có tên mã hàng, số lượng quản lý. Sau cải tiến, công ty tối tư được 50m2 diện tích, giảm thời gian tìm kiếm vật tư, tăng hiệu suất
và qua đó, thuận tiện trong công tác quản lý kho.
Tương tự, công ty cũng áp dụng Kaizen tại giá để phôi tròn. Trước đây, các thanh phôi tròn cũng không gắn tem mác, công nhân rút lấy phôi khó khăn, phải nhấc cây phôi trên mới lấy được cây phối phía dưới và dễ bị dập vào tay, đồng thời, mất thời gian. Để cải tiến, công ty Intech đã ghi đường kính phôi, vật liệu, có phân cách hàng trên với hàng dưới, có ngăn chống lăn.Nhờ đó, việc lấy phôi tròn thuận lợi hơn.
Về dòng chảy sản xuất, các chuyên gia nhận thấy dòng chảy còn zic zắc, vào và ra đi cùng một đường, lãng phí di chuyển, không có kho tồn BTP tạo phôi, lưu thông phôi và việc phân bổ ra các khâu sau bị tắc nghẽn di chuyển. Theo tư vấn của Toyota, layout lại dòng chảy sắp xếp lại máy móc là Tạo phôi – Gia công – Hàn, nhờ đó không lãng phí di chuyển, dòng chảy từ tạo phôi sang bộ phận sau không bị ách tắc. Do đó, công ty tối ưu được 120 m2, giảm 30% quãng đường di chuyển, tốc độ luân chuyển phôi nhanh hơn. Tương tự như vậy tại phòng QC, công ty giảm được 10 phút/tháng cho một nhân sự di chuyển, tiết kiệm 22m2, chuyển sang làm phòng kỹ thuật sản xuất gia công cơ khí.
Tại khu vực điện hóa sản phẩm Inox, các cải tiến đã giúp tiết kiệm từ 9000 giây đến 150 phút/tháng.
Còn nhiều hoạt đông cải tiến tiêu biểu khác như cải tiến máy ép nhiệt cốc bi, từ chỗ chỉ ép 1 được 1 sản phẩm trong 1 chu trình, thời gian chờ rất dài thì nay ép được 3 sản phẩm. Do đó, hiệu suất sản xuất tăng lên rõ rệt. Một ngày, một máy có thể ép tăng từ 800 sản phẩm lên 2000 sản phẩm.
Theo ông Hoàng Hữu Yên, TGĐ Intech, kết quả lớn hơn cả là sự thay đổi về nhận thức của nhân sự. Công ty đã có những thay đổi tích cực về tư duy quản
lý, tư duy về 5S, tu duy về cải tiến; kỹ năng nhìn nhận vấn đề và giải quyết vấn đề được nâng cao; nhân sự tự giác hơn và hiểu về cải tiến MFC, Motion, Karakuri và áp dụng vào thực tiễn sản xuất.
Đại diện ban dự án của Intech chia sẻ, chương trình rất bổ ích và đội ngũ nhân sự đã học được nhiều kiến thức, kỹ năng kinh nghiệm mới áp dụng trong thực tiễn sản xuất. Một điều quan trọng khác là tôi có cơ hội được tiếp xúc với những tư duy mới, tiếp xúc với các chuyên gia nhiều kinh nghiệm thực chiến tại hiện trường, cải tiến chất lượng, hiệu suất. Điều đó khiến cho đội ngũ Intech cảm nhận muốn làm, muốn thay đổi. Đặc biệt, năng lượng tích cực này được lan tỏa từ đội ngũ chuyên gia của Toyota Việt Nam đầy tâm huyết, nhiệt tình, gần gũi, tỉ mỉ, khoa học.
Băng Dương