Công ty TNHH Công nghiệp Haast Việt Nam (trụ sở tại Bắc Từ Liêm, Hà Nội, nhà máy đặt tại Hà Nam) được đầu tư bài bản với tầm nhìn trở thành một trong những thương hiệu đi đầu tại Việt Nam về sản xuất và phát triển các sản phẩm gốc (OEM, ODM) cho lĩnh vực gia dụng thông minh. Sản phẩm chính của công ty là quạt điện, đồ gia dụng, linh kiện ô tô.
Cũng như nhiều doanh nghiệp công nghiệp hỗ trợ khác của Việt Nam, trước đây, hiện trạng nhân sự của công ty còn thiếu về các khái niệm trong phương pháp tổ chức sản xuất tinh gọn, hiệu quả. Nhận thức về 5S, hiểu biết về MFC, Karakuri, Motion và kỹ năng cải tiến yếu. Trong nhà xưởng, vật tự, BTP để lộn xộn, không qui định. Các công nhân phải làm nhiều thao tác khó trong dây chuyền như phải cúi, với, tìm kiếm sản phẩm. Dòng chảy sản xuất cũng không tối ưu và liền mạnh. Tồn kho trong từng công đoạn sản xuất còn lớn.
Theo tư vấn của Toyota Việt Nam, Hasst đã lập Ban điều hành dự án cải tiến do trực tiếp Tổng giám đốc Dương Nguyên Thành làm trưởng ban.
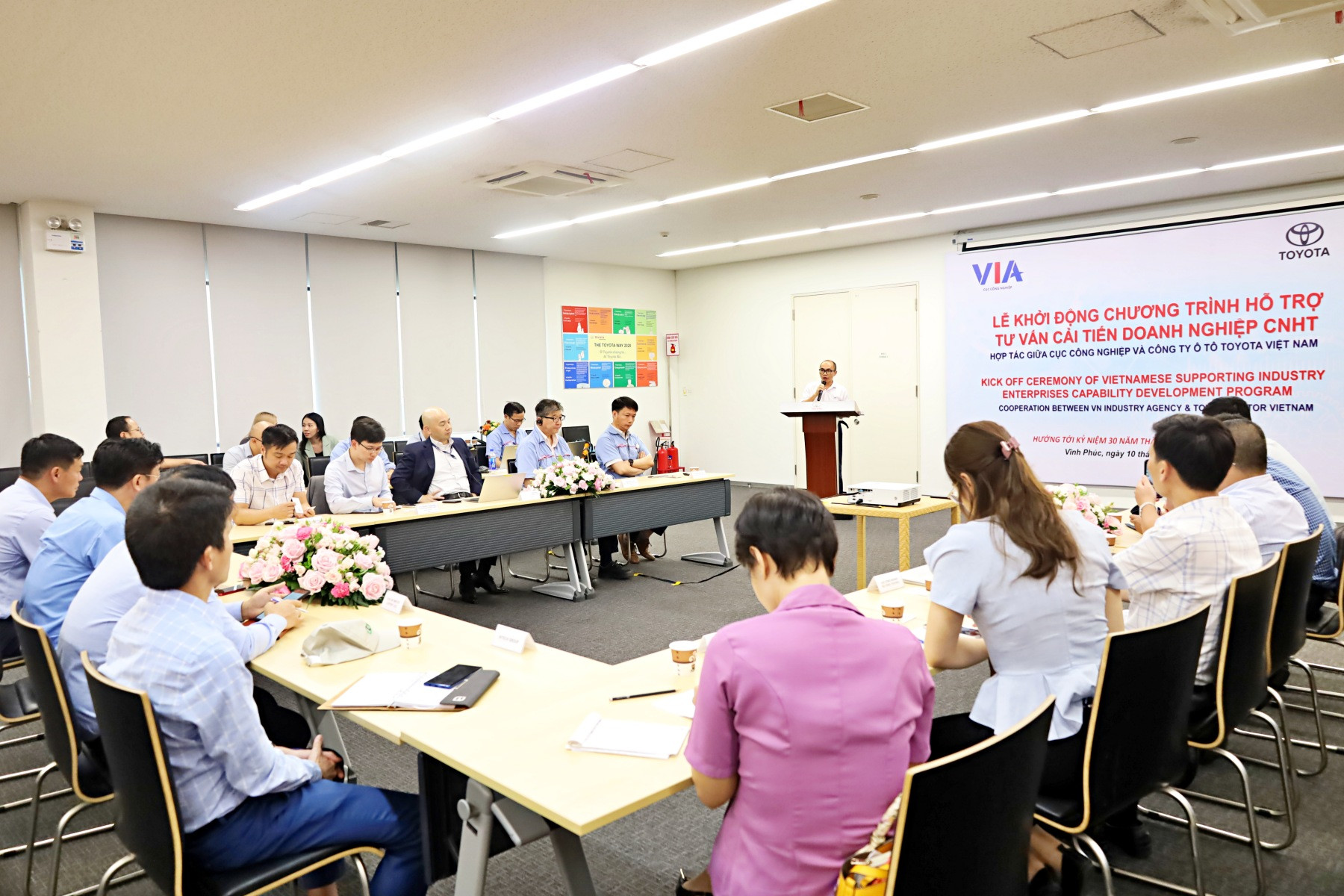
Kết quả tổng hợp hoạt động cả tiến Karakuri theo phương pháp tổ chức sản xuất tinh gọn của Nhật Bản, công ty đã giảm 5 nhân sự trong quy trình lắp ráp quạt, tăng 40% năng suất. Diện tích sản xuất tiết kiệm tới 580 m2. Ban lãnh đạo công ty đã áp dụng 16 tiêu chí của Toyota vào hoạt động, đạt nhiều kết quả đáng ghi nhận.
Một vài ví dụ cho hoạt động cải tiến Kaizen được nêu ra cho thấy diện mạo nhà xưởng đã thay đổi hoàn toàn. Ví dụ, việc để vật liệu nhựa trước đây còn lộn xộn, công nhân rất dễ nhầm lẫn các loại nhựa với nhau, nhưng sau cải tiến, layout cải tiến, công nhân đã dễ dàng tìm kiếm các loại nhựa, bên trong nhà máy sạch sẽ gọn gàng hơn.
Tương tự, dòng chảy sản xuất của công ty cũng không tối ưu. Trước đây, vị trí khâu bộ phận kỹ thuật và bán thành phẩm cách xa nhau, hàng tồn kho phòng in quá nhiều, diện tích lưu kho bán thành phẩm lớn. Ở hệ thống dòng chảy sản xuất chi tiết ông, công nhân huy động quá nhiều lên tới 13 người trong 1 line trong khi công nhân đứng máy chờ đợi nhiều. Dòng chảy sản xuất bị zic zac, lãng phí.
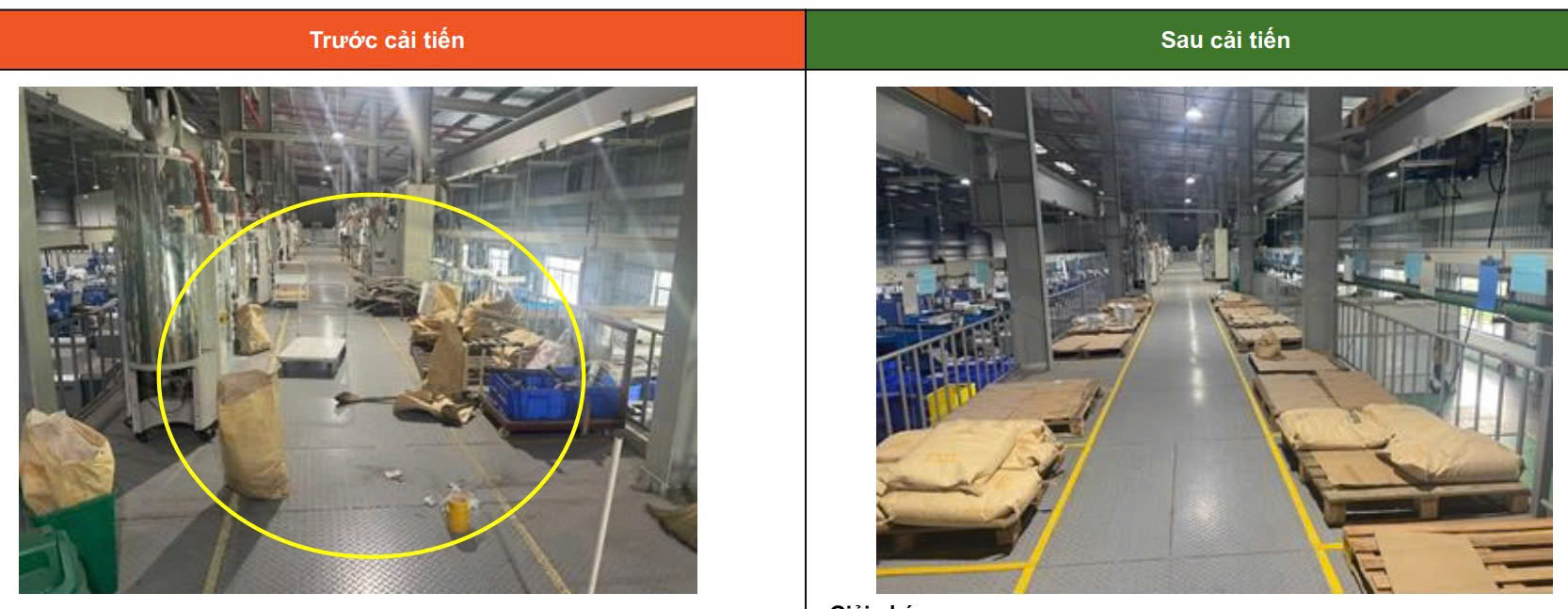
Sau khi áp dụng phương pháp Kaizen, các nhân công có thời gian trống đứng máy được sắp xếp lại, bổ sung việc lắp ráp linh kiện. Khâu lắp ráp sản phẩm được thực hiện ngay sau khi sản phẩm đúc xong. Nhờ đó, năng suất tăng vọt lên 40%, số nhân công giảm xuống 5 người. Nhà máy theo đó tiết kiệm được 150m2 diện tích lưu kho bán thành phẩm, 200m2 lưu kho thành phẩm và 30m2 line lắp ráp.
Một ví dụ khác, tại khu vực để vật tư, trước đây, công nhân phải cúi lấy sản phẩm rất khó mất thời gian. Sau đó, theo tư vấn cải tiến, công ty đã làm giá để vật tư, triệt tiêu thao tác cúi lấy sản phẩm. Một cải tiến nhỏ này giúp cho công ty tiết kiệm tới 80 phút/tháng.
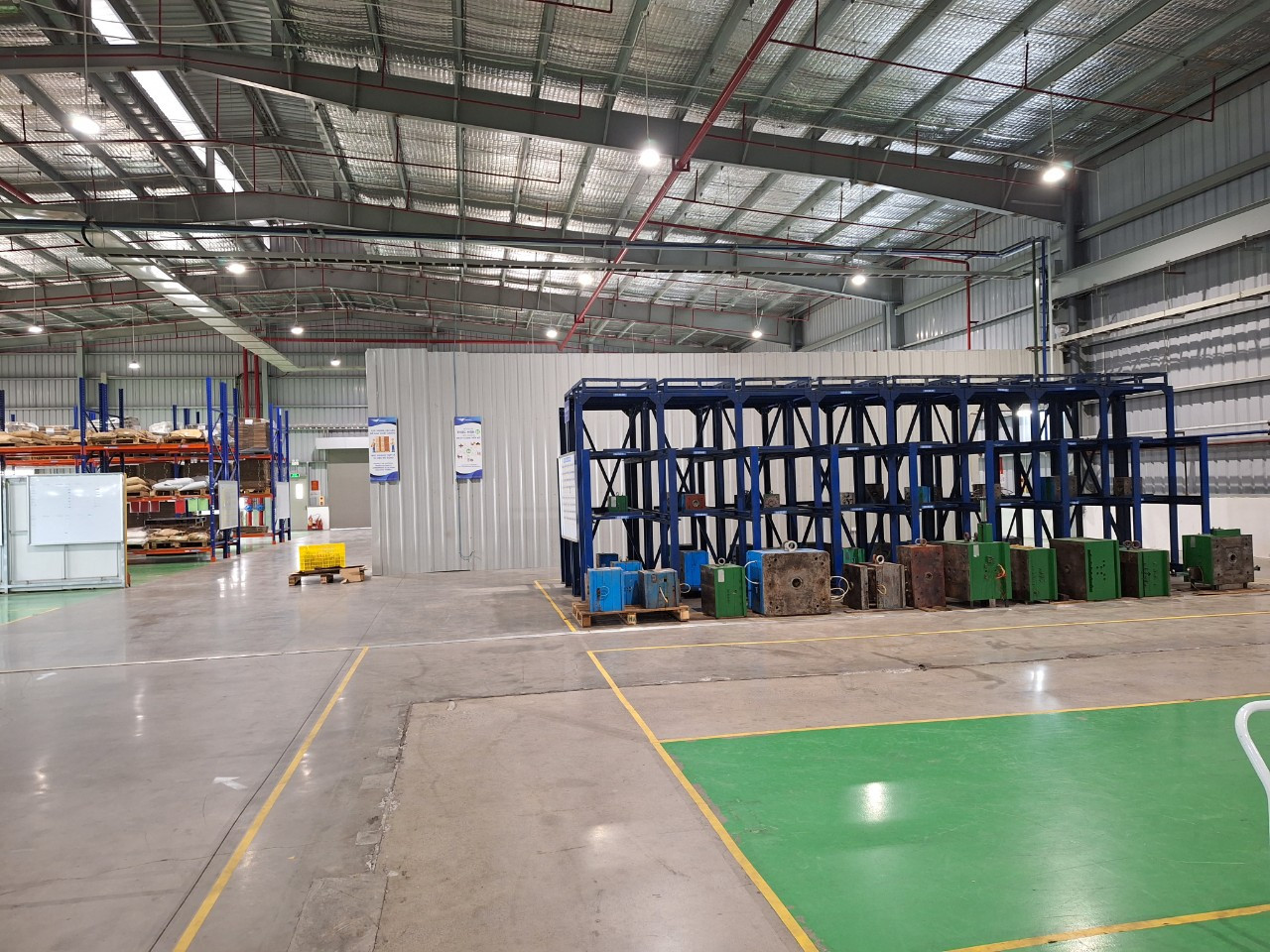
Trước đây, nhân viên phải cúi người, xoay chi tiết 90 độ để đặt part vào jig, nay, công ty cải tiến làm 1 xe giá để part ngay cạnh vị trí thao tác, công nhân chỉ xoay chi tiết 45 độ, để đặt part vào jig, giảm hẳn thao tác xoáy, cúi cho nhân viên.
Khâu lấy phôi của nhân viên trước đây ước mất 28h/tháng, sau cải tiến, chỉ còn mất 18h/tháng. Nhân viên không phải cúi, với nhiều lần lấy hàng và dễ tìm hàng hơn. Tại khu vực giao hàng, trước đây, công ty cần 7 người để chuyển hàng vào container, thao thác nặng nhọc nhưng sau cải tiến, áp dụng cơ chế mặt phẳng nghiêng của karakuri + roller để làm băng chuyền chuyển hàng, công đoạn này giảm đi 4 người cho mỗi lần giao hàng. Hiệu quả năng suất lao động tăng lên rõ rệt.
Chương trình đào tạo cải tiến của Toyota đã mang đến cho Haast những kiến thức và kỹ năng vô cùng quý báu. Báo cáo kết quả quá trình cải tiến sản xuất trên, ông Dương Nguyên Thành, Tổng giám đốc Công ty Hasst Việt Nam chia sẻ: “Qua chương trình, đội ngũ của chúng tôi đã được trang bị những công cụ và phương pháp quản lý sản xuất hiện đại, đặc biệt là triết lý Kaizen. Nhờ đó, chúng tôi đã phát hiện và khắc phục được nhiều điểm yếu trong quy trình sản xuất, từ đó nâng cao hiệu suất làm việc và giảm thiểu lãng phí”.
“Các buổi thực hành và thảo luận nhóm đã tạo ra một môi trường học tập năng động, giúp chúng tôi hiểu sâu hơn về các khái niệm và áp dụng chúng vào thực tế”, ông Thành nói.
Ông bày tỏ: “Chúng tôi đánh giá cao sự tận tình và chuyên nghiệp của các chuyên gia Toyota. Chương trình này không chỉ là một khóa học, mà còn là một hành trình giúp chúng tôi không ngừng cải tiến và phát triển. “Sau khi hoàn thành chương trình đào tạo cải tiến của Toyota, chúng tôi mong muốn xây dựng Haast một tổ chức học hỏi liên tục, nơi mỗi cá nhân đều được trao quyền để đóng góp ý tưởng và sáng tạo. Thông qua chương trình đào tạo, chúng tôi sẽ tập trung vào việc cải thiện quy trình làm việc, giảm thiểu thời gian giao hàng và tăng cường sự hài lòng của khách hàng, nâng cao năng suất và chất lượng sản phẩm, đồng thời mang đến cho khách hàng những trải nghiệm tuyệt vời.
“Cuối cùng, chúng tôi tin rằng việc áp dụng thành công các nguyên tắc của Toyota sẽ giúp công ty chúng tôi đạt được sự tăng trưởng bền vững và trở thành một đối tác của Toyota trong tương lai gần”, Tổng giám đốc Hasst Việt Nam nhấn mạnh.
Băng Dương